Automatic deburring for engine turbine
The importance of deburring in the aerospace industry
Because of the extreme conditions in which they are used, engine parts require expensive manufacturing techniques to achieve a flawless finish. Each manufacturing operation, whether forging, moulding or machining, generates defects known as burrs. These irregularities could be a source of injury during handling and could compromise operation.
Strict tolerances and specific surface finishes are of great importance, as these parts are subjected to extreme conditions of temperature and pressure.
Precision deburring is therefore essential to eliminate burrs that could alter critical dimensional tolerances, as well as to create shapes (chamfers or calibrated radii).
What’s more, the complex materials used for these parts are constantly evolving to meet new industry requirements, such as reducing the carbon footprint. This accentuates the need for high-precision deburring to adapt to new designs and ensure that every component meets the most stringent quality criteria.
Deburring is the finishing method used to remove these surface details. By deburring, the surfaces of objects can be made more homogeneous, allowing subsequent grinding or polishing steps to be carried out.
But manual deburring then reaches these limits for this type of application.
Angle-breaking is the finishing method used to remove problems.
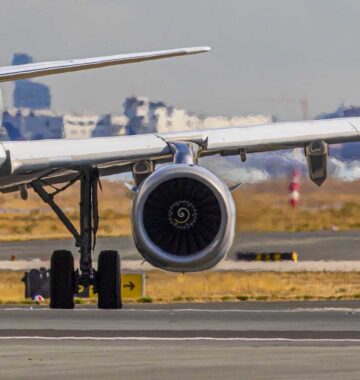
The advantages of automatic deburring
Robotic deburring represents a major technological advance in the optimisation of manufacturing processes for complex parts such as aircraft engines. By integrating automated systems, it becomes possible to effectively replace manual deburring (which is time-consuming and arduous, exposing operators to health risks), while improving quality and productivity.
Increased output and reduced costs
Thanks to the speed and efficiency of robotic systems, cycle times are reduced, making it possible to increase overall production output by increasing opening times (nights, weekends). In addition, these systems consume less abrasives or cutting tools than manual methods, reducing operating costs. This has a direct impact on profitability by speeding up delivery times while maintaining high levels of quality.
Improved access to parts with complex geometries
Some parts, particularly those used in aircraft engines, have highly complex geometries that are difficult or impossible to manually deburr. Robots can quickly and consistently access every point on the part, ensuring accurate deburring, whatever the design or configuration of the part.
Reducing the risk of injury and improving working conditions
Manual deburring is not only time-consuming, but also exhausting for operators. It presents a high risk of musculoskeletal disorders (MSD) linked to repetitive movements, as well as the risk of breathing carcinogenic dust from the materials. Automating this task not only eliminates this risk, but also allows operators to concentrate on less demanding and more rewarding tasks, thereby improving safety and the working environment.
Improved quality and repeatability
One of the main advantages of robotic deburring is the consistency of the results. Unlike manual deburring, where human variations can introduce errors, automation ensures consistent quality. It does not only remove burrs with precision, it also ensures repeatability of operations, even on the most complex contours.
Automatic deburring not only ensures higher output, but also optimises both the quantity and quality of production.
GEBE2 robotic technology: tailor-made solutions for deburring your parts
GEBE2, a specialist in robotic integration, provides turnkey robotic cells designed to meet the demanding requirements of industries such as aerospace. Thanks to its customised approach and advanced expertise, GEBE2 enables its customers to optimise their deburring processes.
Flexible options tailored to customer needs
GEBE2 robotic cells are highly customisable, with different options to suit the specific needs of each customer:
- Rotary, vertical or horizontal end-effectors or tools magazines for fast, efficient tool and end-effector
- Deburring of several types of part in the same
- Ergonomic workpiece loading for improved safety and
- Integrated vision and measurement systems for precise positioning and real-time quality
Integration and customisation of robotic cells
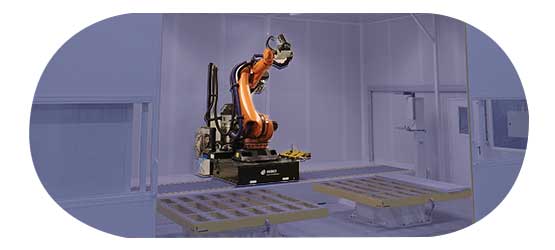
Demonstrators
GEBE2 supports its customers in developing customised solutions thanks to a complete robotics platform, equipped with test cells and demonstrators. This platform enables the feasibility of processes to be tested by drawing up test programmes with customers. A dedicated R&D/feasibility team works closely with customers to define and carry out the tests, and provides detailed reports (videos, photos, analyses).
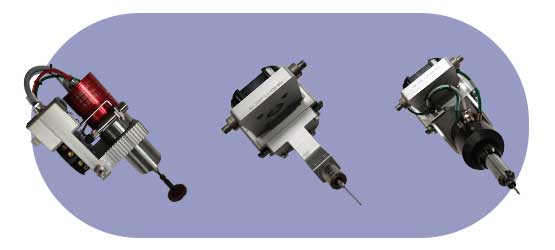
Effectors
GEBE2’s expertise also extends to the selection of abrasives, cutting tools and robotic equipment (robots, compliances, electro-spindles, etc.), in order to offer the best solution for each application. Specific end-effectors (machining, probing, brushing, etc.) can be developed according to requirements, with design, manufacturing and prototype development services.
Innovations and derivatives of the deburring process
GEBE2 does not limit itself to traditional deburring. The company is developing derivative processes to meet the most complex applications, enabling the cell to adapt itself automatically to variations in part geometry, and the robot trajectory to evolve automatically.
Advanced programming and regular movements
To guarantee high-quality deburring, the consistency of tool movements is crucial. GEBE2 offers advanced programming solutions with full path simulation using high-performance software such as Robotstudio, Kukasim and Robotmaster.
These offline programming tools (PHL) enable trajectories to be simulated and movements to be optimised before going into production, thereby limiting programming time and the risk of collisions.
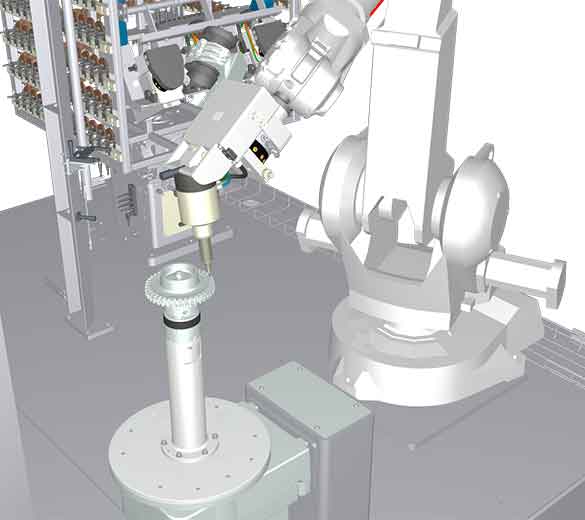
Examples of automated deburring machines
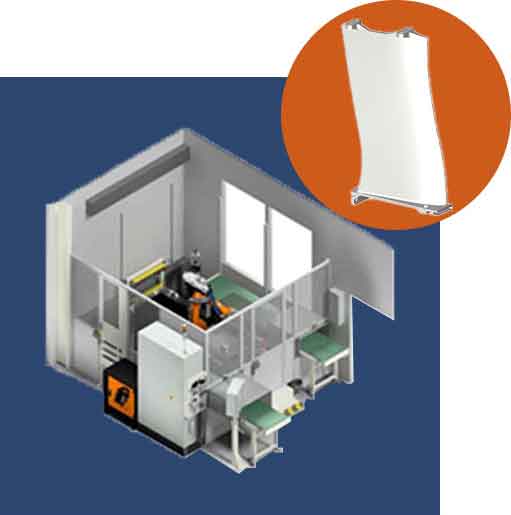
Deburring of aluminium OGV arms
GEBE2 has developed a robotised cell dedicated to the deburring of aluminium OGVs, essential components of aircraft engines.
OGV arms are often made of aluminium for their lightness and resistance to corrosion.
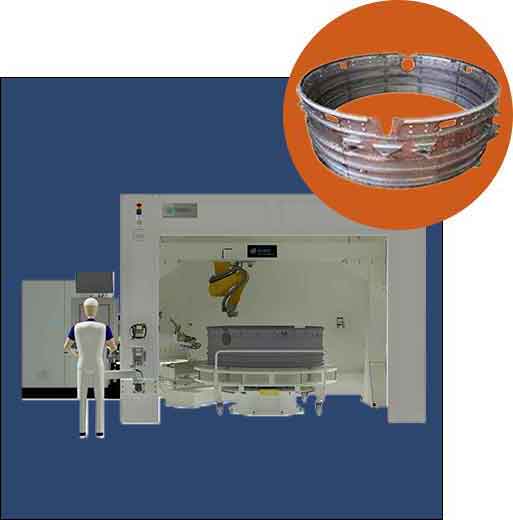
Large-scale deburring of a titanium housing
GEBE2 has designed a robotic cell to deburr a 2-metre diameter titanium housing, a critical part for LEAP engines used in the aerospace industry. This large housing requires precision and rigorous tolerances because of its role in the engine’s structure.
Deburring operations on large parts, such as the housing, require regular movements and controlled effort to avoid damaging the surface, while effectively removing burrs. In addition, the complex geometry of the part and its large diameter require appropriate handling and processing solutions : rotary table, 6-axis industrial robot, electro-spindles, compliances, abrasive and cutting tools storage magazine, vision, etc.
All the robot’s trajectories have been simulated beforehand to ensure optimum deburring from the very first cycles.